
Het continu verbeteren van logistieke processen
Het continu verbeteren, heeft tot doel de kwaliteit en de prestaties van een product of proces te verhogen, door een voortdurende analyse van de daarbij behorende elementen. Deze techniek, van oorsprong afkomstig uit Japan, wordt steeds populairder bij westerse bedrijven. Continu verbeteren zorgt voor betere prestaties door voortdurend kleine veranderingen aan te brengen, teneinde onrendabele praktijken te elimineren en voorschriften te standaardiseren.
In dit artikel bespreken we het concept van het continu verbeteren, de belangrijkste strategieën en de toepassing ervan in de logistieke sector.
Het continu verbeteren
Continu verbeteringstechnieken zijn een reeks strategieën die gericht zijn op het verbeteren en optimaliseren van procedures, producten of diensten door middel van kleine aanpassingen, die het resultaat zijn van een grondige vakkennis en analyse van de gegevens.
Er bestaan verschillende methoden om de prestaties van logistieke processen te verbeteren op basis van de strategie van het continu verbeteren. De Kaizenmethode of de «5S» is echter één van de meest populaire processen geworden vanwege de eenvoud en doeltreffendheid.
Continu verbeteren door middel van Kaizen
Kaizen (Japans voor "veranderen naar beter" of "verbetering") is een methode ontwikkeld door de Japanse ingenieur Taiichi Ohno voor de autofabrikant Toyota na het einde van de Tweede Wereldoorlog. De functie ervan was het concurrentievermogen van het merk te vergroten en het af te stemmen op dat van de Amerikaanse fabrikanten. Dit concept is inmiddels wereldwijd een standaard geworden in het bedrijfsmanagement.
De Kaizen-methode is gebaseerd op het principe dat het altijd mogelijk is een proces te verbeteren, zelfs als het correct functioneert. Deze strategie, die vooral op de productie en de logistiek wordt toegepast, maakt gebruik van een reeks procedures om de werking van het bedrijf te analyseren, ondoelmatigheden op te sporen en veranderingen door te voeren. Het draait om vijf principes, die bekend staan als de 5S, vanwege hun oorspronkelijke Japanse benamingen:
- Seire (sorteren): het eerste proces in de Kaizen-methode betreft het analyseren van de taken om die werkzaamheden te onderscheiden die waarde toevoegen aan het product of de dienst (deze taken worden gemba genoemd).
- Seiton (ordenen): de medewerker moet over alle instrumenten beschikken om flexibel en productief te zijn. Het toepassen van Seiton bestaat uit het organiseren van ploegen teneinde ondoelmatige verplaatsingen of handelingen te vermijden.
- Seiso (schoonmaken): het opsporen van tekortkomingen en het schoonmaken van de werkplek zijn van essentieel belang om ervoor te zorgen dat de magazijnmedewerker zich comfortabel voelt en zo goed mogelijk zijn werk kan doen.
- Seiketsu (normaliseren): na de identificatie van de tekortkomingen moeten de nodige regels of procedures worden vastgesteld om de efficiëntie van de processen te verbeteren.
- Shitsuke (disciplineren): deze laatste stap is van fundamenteel belang voor het welslagen van de vorige vier. Het houdt in dat de hele organisatie zich ertoe verbindt de nieuwe regels te integreren en een filosofie van voortdurende verbetering toe te passen om de waarde van de activiteiten te verhogen.
Kortom, de 5S Kaizen-methode is een ideale strategie om de rentabiliteit van uw organisatie te verhogen, eventuele tekortkomingen op te sporen en te corrigeren en, vooral, elke mogelijke bron van toegevoegde waarde te ontwikkelen.
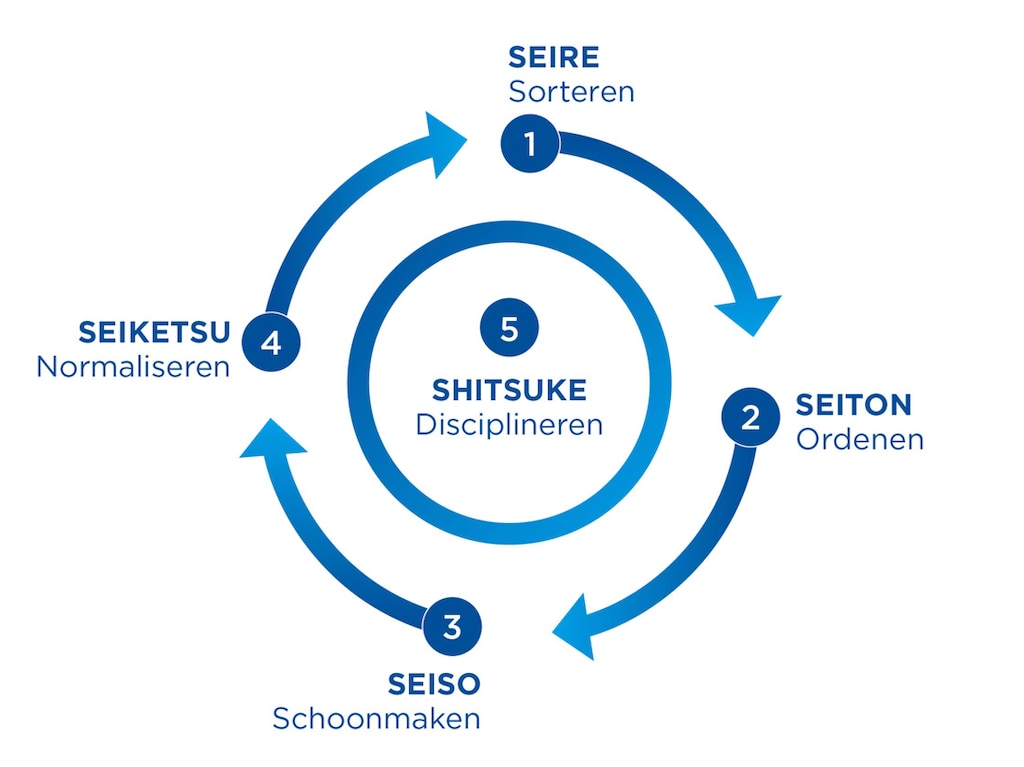
Andere methodes voor continu verbeteren: van de kwaliteitscirkel van Deming tot Six Sigma
Naast de 5S-methode zijn er nog andere strategieën en hulpmiddelen voor het continu verbeteren. De prioriteit ligt in het bereiken van proces-excellentie door middel van de gegenereerde informatie. Tot de andere belangrijke methoden om voortdurende verbetering te normaliseren behoren:
- De Deming cirkel ou PDCA: PDCA is het Engelse acroniem voor: Plan, Do, Check, Act. Deze cyclische strategie beschrijft de vier essentiële stappen om ondoelmatigheden op te sporen, oplossingen uit te werken en uiteindelijk de winstgevendheid van de magazijnprocessen te verbeteren.
- Six Sigma: deze techniek van voortdurende verbetering bestaat erin fouten te voorkomen bij de levering van het eindproduct aan de klant. Er wordt gestreefd naar maximaal 3,4 fouten per miljoen kansen, waarbij een vergissing wordt gedefinieerd als een incident dat kan leiden tot ontevredenheid bij de klant.
- Lean Six Sigma: de strategie Lean Six Sigma is gebaseerd op de identificatie van alle stappen die geen waarde toevoegen aan het eindproduct, teneinde een product van de hoogste kwaliteit te verkrijgen.
Om continu te verbeteren is het niet nodig te kiezen tussen de verschillende methoden, want geen enkele methode is beter dan de andere, ze vullen elkaar aan en elke aanpak heeft zijn voordelen. Alle strategieën kunnen en moeten gelijktijdig worden toegepast. Het doel is het continu verbeteren van logistieke processen: ondoelmatigheden te verminderen, stapsgewijze veranderingen door te voeren en ervoor te zorgen dat nieuwe gewoonten in het bedrijf worden opgenomen.

Verspillen: muet, mura, muri
Het continu verbeteren van processen betekent dat deze voortdurend worden geanalyseerd om in elke fase een optimale efficiëntie te garanderen. Zo omvatten de termen muda, mura en muri een strategie om vergissingen en verspillingen in de productie op te sporen.
Dit systeem, ook bekend als het 3M van het Toyota Productie Systeem, is gebaseerd op de analyse van vergissingen en verliezen in een productieproces om, door middel van veranderingen in de organisatie, zonder tekortkomingen te kunnen produceren en de beste klantervaring te kunnen garanderen. De drie sleutelbegrippen:
- Muda (verspilling): vergissingen die middelen verspillen en geen waarde aan het product toevoegen. Oorspronkelijk omvatte de Toyota-methode 7 veel voorkomende verliezen in een productie-eenheid: onnodige verplaatsingen, overtollige voorraden, dubbele handelingen, overproductie, onnodige wachttijd tussen de verschillende productielijnen, excessieve verwerkingen die geen waarde toevoegen en inefficiënt vervoer.
- Mura (ongelijkheid): de productiemanager moet ongelijkheden, onderbrekingen of veranderingen in de werklast opsporen die tot extra productiekosten leiden. Dit vereist een uitvoerige doorlichting van de resultaten van de productieprocessen, om tekortkomingen, vergissingen of wanprestaties op te sporen. Hoe kunnen deze onregelmatigheden worden opgelost? Door de implementatie van methoden waarmee de productie kan worden afgestemd op de vraag, zoals de Kanban of de just-in-time methode.
- Muri (te veel): het geheel aan soorten verliezen gevormd door de muda (verspilling) en de mura (ongelijkheid) veroorzaakt wat de Japanners aan muri (te veel) toeschrijven, namelijk stress. Een slechte planning leidt tot vermoeidheid van de magazijnmedewerker en zelfs tot knelpunten in de productielijnen.
Kortom, door de Toyota 3M-methode stap voor stap toe te passen, worden verspillingen bij de productie en overbelastingen en onevenredige verdelingen in de werklast tegengegaan. Het uitbannen van zowel muda (verspilling) als mura (ongelijkheid) leidt dus tot het uitbannen van muri (te veel), dat wil zeggen van stress en onevenredige verdelingen in de productielijnen.
De voordelen van het continu verbeteren van logistieke processen in het magazijn
Hoe kan het continu verbeteren van de logistieke processen en van de dagelijkse werkzaamheden in het magazijn u verder helpen? De belangrijkste voordelen:
- De garantie van een kwaliteitsproduct/dienst: de toepassing van een techniek van het continu verbeteren van processen, garandeert het succes van de productie of de logistiek, wat een betere klantervaring met zich brengt.
- Vermindering van de logistieke kosten: deze strategie maakt het mogelijk de magazijnvoorraden te optimaliseren, de doorlooptijd voor leveranciers te verkorten, prioriteit te geven aan de meest productieve activiteiten en onrendabele werkzaamheden te schrappen.
- Nuttige verplaatsingen: methoden zoals Kaizen of de kawaliteitscirkel van Deming (PDCA) voorkomen onnodige verplaatsingen en stellen efficiëntere verzamelroutes voor, waardoor de productiviteit van de operators toeneemt.
Naast deze verbeteringen vergemakkelijkt de invoering van deze systemen de integratie van een "pull flow"-mentaliteit in de faciliteiten. Dit betekent dat magazijnprocedures werken volgens het JIT-principe (just-in-time), waarbij taken worden uitgevoerd wanneer er vraag is vanuit de klant, zodat inefficiënte werkzaamheden en het risico van te grote voorraden of achterhaalde goederen worden vermeden.
Mecalux heeft meerdere oplossingen die de implementatie van een continu verbetermethode zoals Kaizen of de cirkel van Deming ondersteunen. Supply Chain Analytics, de geavanceerde module van Easy WMS, stelt de logistiek manager in staat alle gegevens van het magazijn te verzamelen en deze informatie te structureren om relevante logistieke KPI's te creëren en de impact van het continu verbeteren van de logistieke processen te meten.

Continu verbeteren om het concurrentievermogen te garanderen
In een context waarin de logistiek voortdurend in ontwikkeling is, met technologieën die in de nabije toekomst mogelijk een revolutie in het dagelijkse leven van bedrijven teweeg zullen brengen, is het van essentieel belang om strategieën voor het continu verbeteren van processen in te voeren, teneinde concurrerend te blijven.
De eerste stap naar een succesvolle Supply Chain is het monitoren en analyseren van de KPI's van uw magazijn om storingen te identificeren en processen die geen waarde toevoegen te schrappen. Het implementeren van een continu verbeteringsstrategie in een bedrijf, is de enige manier om de logistieke kosten te verlagen en de beschikbare middelen te optimaliseren.
Als u de resultaten van uw magazijn wilt optimaliseren, neem dan contact met ons op. Onze experts helpen u graag het beste uit uw logistiek te halen.