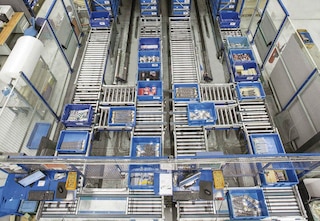
Definitie en toepassing van de Kanban-methode in de logistiek
De Kanban-methode organiseert de levering en productie van goederen, waarbij de productieprocessen functioneren op basis van just-in-time (JIT), wat betekent dat grondstoffen worden geleverd op het exacte moment dat ze nodig zijn. Het uiteindelijke doel is de productiecapaciteit af te stemmen op de vraag, om overtollige voorraden en onnodige wachttijden tussen processen te vermijden.
De Kanban-methode werd in de jaren '50 door het Japanse bedrijf Toyota ontwikkeld, en maakt deel uit van de Lean Manufacturing methodologie, die is gericht op het verhogen van de productiviteit, door verspilling te minimaliseren. Dit productiemodel, ontwikkeld door industrieel ingenieur Taiichi Ohno, bleek dé oplossing te zijn voor de diepe depressie, waarin de Japanse industrie na de Tweede Wereldoorlog was gezonken.
Wat is de Kanban-methode? Definitie en oorsprong
De Kanban-methode voorziet in een protocol voor het aanvullen van de voorraden. Het betreft een systeem voor het doorgeven van opdrachten voor productie en bevoorrading van materiaal. Het wordt gebruikt in productiemodellen die rechtstreeks op de vraag reageren: het «Pull-model». Hierbij komt de productie van het product pas op gang, wanneer de uiteindelijke bestelling van de klant is ontvangen.
Taiichi Ohno ontwierp het Kanban-systeem op basis van de bevoorradingsregels van Amerikaanse supermarkten. In deze winkels halen de klanten de producten met een tag uit de rekken, en bij het passeren van de kassa verzamelt het systeem alle verkochte referenties, waarna het een bevoorradingsorder geeft aan het magazijn, dat de goederen op dezelfde manier identificeert. Zodra de artikelen in de supermarkt zijn aangevuld, stuurt het magazijn op zijn beurt een bevoorradingsorder naar de leveranciers of fabrikanten. Dit loopt door de hele toeleveringsketen heen. Het systeem, gebaseerd op het bestelpunt, wordt gebruikt om te bepalen wanneer bevoorradingsorders moeten worden geplaatst.
Hoe het werkt. Kanban-tags en tabellen
In het Japans betekent Kanban letterlijk «gekleurde kaarten». Oorspronkelijk werden kartonnen kaartjes gebruikt, om de nodige elementen uit het vorige proces aan te vragen. Zodra de bevoorrading was voltooid, werd de Kanban-kaart in de oorspronkelijke bak teruggelegd.
Deze kaarten of tags bevatten informatie ter identificatie van alle partijen materiaal : SKU code, partijgrootte, bestemming van de artikelen en de klant die het verzoek heeft ingediend. De tags werden bevestigd aan elke laadeenheid of schap, waarin of waarop het product zich bevond.
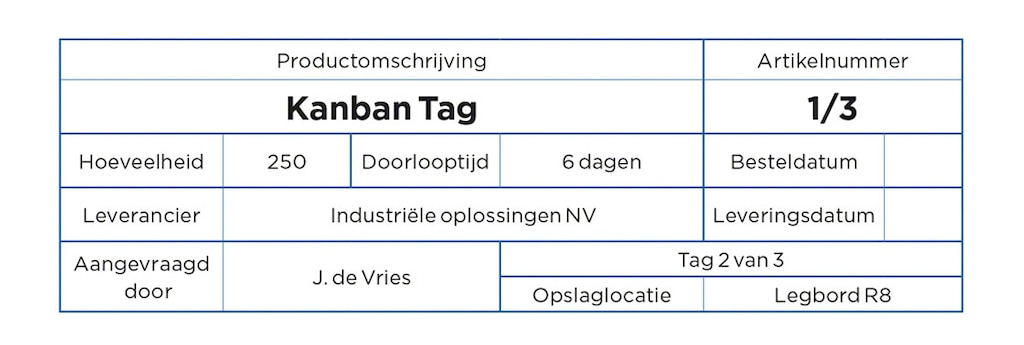
Tegenwoordig is het Kanban-systeem vervangen door computertoepassingen die het bevoorradingsproces op gang brengen. Het systeem kan ook worden weergegeven met Kanban-borden, die bestaan uit verschillende kolommen waarop virtuele kaarten of tags worden geplaatst. Zo geeft elke kolom de status van elke taak weer, evenals de persoon die verantwoordelijk is voor de uitvoering ervan.
Hoewel de Kanban-methode oorspronkelijk in een industriële context ontstond, wordt deze tegenwoordig toegepast op het beheer van allerlei soorten projecten, waaronder softwareontwikkeling.
Soorten Kanban-tags
Er bestaan hoofdzakelijk twee soorten Kanban-tags:
- Handling of Transport Kanban: deze tag geeft de hoeveelheid producten aan die moet worden aangevuld, om te voldoen aan de behoeften van het volgende niveau van de toeleveringsketen of Supply Chain. Nemen we het voorbeeld van een supermarkt, dan zou de Handling of Transport Kanban tag, gebruikt worden om aan te geven, dat een product verkocht is en van het magazijn naar de winkel moet worden overgebracht.
- Productie Kanban: deze tag wordt gebruikt om de productie van een product aan te vragen. Als we hetzelfde voorbeeld nemen, zou dit type Kanban-tag, door het magazijn worden afgegeven wanneer er een voorraadtekort is, aangezien de producten al naar de winkel zouden zijn gestuurd.
Het volgende schema toont op schematische wijze de ketenwerking van de Kanban-kaarten voor productie en transport op een vereenvoudigde productielijn:
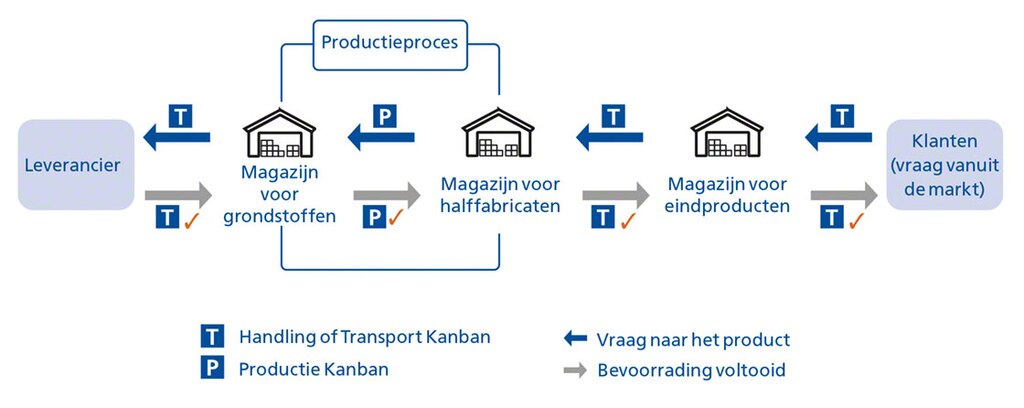
De voordelen van de Kanban-methode in de logistiek en de productie
De Kanban-methode is de perfecte bondgenoot van het just-in-time systeem, omdat het:
- De voortgang van het werk visueel maakt en gemakkelijk elke fase van de productie- of bevoorradingscyclus kan identificeren.
- Gemakkelijk limieten vast stelt voor work in progress (WIP), zodat knelpunten worden vermeden.
- De doorlooptijd tussen processen meet, d.w.z. de tijd die nodig is om elke fase te voltooien.
- Toezicht houdt op de productie en het beschikbare materiaal in de verschillende opslaglocaties.
- Overproductie of overtollige voorraad voorkomt, wat een winst aan opslagruimte betekent.
Nadelen van het gebruik van het Kanban-systeem
Deze methode is niet altijd de meest geschikte, omdat er bepaalde beperkingen aan verbonden zijn.
- Het Kanban-systeem geeft optimale resultaten, wanneer de productiestroom gelijkmatig over het jaar is verdeeld, en in korte reeksen van gelijke volumes is georganiseerd. Als de vraag in het bedrijf echter sterk fluctueert, waardoor de productie plotseling moet worden aangepast, heeft de Kanban-methode zijn beperkingen en wordt het gebruik ervan afgeraden.
- Als er ergens in de productieketen een probleem optreedt, kan deze methode tot verdere vertragingen leiden.
- Dit systeem is niet het meest flexibele om grote veranderingen in productietechnieken op te vangen.
- Het werkt niet goed als leveranciers niet dezelfde Kanban-regels voor bevoorrading aanhouden.
Kanban in een magazijn gebruiken. De functie van een WMS
In magazijnen maakt de Kanban-methode niet langer gebruik van kartonnen kaartjes: bedrijven gebruiken het nu via een warehouse management systeem, zoals Easy WMS, gecombineerd met automatische identificatiesystemen zoals streepjescodes of RFID. Elk bestand in het WMS functioneert als een Kanban-tag omdat, wanneer de gegevens door een scanner worden gelezen, het systeem alle informatie met betrekking tot het betreffende artikel terugzendt.
In de logistiek wordt deze methode gebruikt om de bevoorrading op verschillende niveaus te organiseren:
Kanban in één magazijn
Als de zones voor picking en opslag gescheiden zijn, is het Kanban-systeem bijzonder geschikt voor de bevoorrading van de pickingstellingen.
Wanneer de referenties van deze picking zones uitgeput zijn, geeft het WMS een automatische waarschuwing voor bevoorrading af, die functioneert als een Kanban-tag. Wanneer een magazijnmedewerker een tekort aan materiaal constateert, kan het ook handmatig worden geactiveerd.
Op die manier wordt de verplaatsing van goederen gepland volgens prioriteit, hoewel het meestal wordt gereserveerd voor de daluren in het magazijn, bijvoorbeeld voor «wave picking».
Als tijdens het verplaatsen van goederen van de opslaglocatie naar de picklocatie, wordt geconstateerd dat artikelnummers zijn uitverkocht, dan kan het WMS een directe melding sturen naar de inkoopafdeling, zodat deze hier rekening mee kan houden bij het doorgeven van bestellingen aan de betreffende leveranciers.
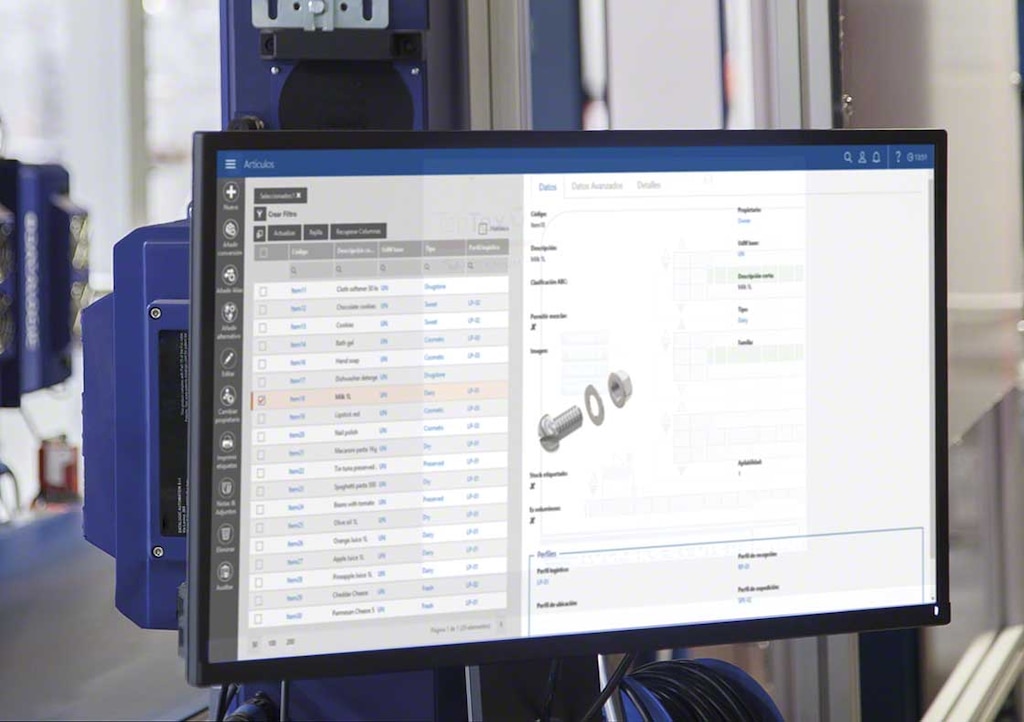
Kanban in een netwerk van logistieke magazijnen
De Kanban-methode kan ook worden gebruikt door bedrijven, die werken met voorraden die over verschillende magazijnen zijn verspreid. Deze kunnen dezelfde productielijn bedienen (zoals bij productielogistiek) of deel uitmaken van hetzelfde logistieke netwerk (zoals bij logistieke netwerken voor de detailhandel).
Hieronder wordt uiteengezet hoe de Kanban-methode werkt in elk van deze gevallen, en welke functies het WMS vervult:
- Toepassing van het Kanban-systeem in produktiemagazijnen: de magazijnen die de fabrieken bevoorraden, en voorraden beheren die ingedeeld zijn naar grondstoffen, halffabrikaten en eindprodukten. Om ervoor te zorgen dat er tijdens het productieproces geen voorraadtekorten ontstaan, is het van essentieel belang automatisch voorraadbeheer te hanteren. Het Warehouse Management Systeem werkt volgens de Kanban-methode, daar het WMS bij een nieuwe bestelling productieorders uitvaardigt, en voor elke referentie de beschikbare veiligheidsvoorraad controleert.
- Toepassing van de Kanban-methode in de toeleveringsketen van de detailhandel: in dit geval wordt het logistieke netwerk gevormd door centrale en regionale magazijnen en fysieke winkels. Overeenkomstig de Kanban-methode wordt de vraag naar producten geregistreerd in de winkel van waaruit de bevoorradingsorders voor het magazijn worden verzonden. In dit geval fungeert het WMS als een bevoorradingskatalysator tussen de verschillende centra, aangezien het de globale voorraadgegevens bevat. Bovendien, als we het voorbeeld nemen van de Store Fulfillment module van Easy WMS van Mecalux, dan maakt deze de organisatie en classificatie van voorraadstromen tussen verschillende centra mogelijk, zonder tussenpersonen, waardoor de logistieke capaciteit van het bedrijf optimaal wordt benut.
Voorraadbeheer met de Kanban-methode
De toepassing van het traditionele Kanban-systeem met grote voorraden, verspreid over verschillende centra, waarbij een bijzonder hoog volume van SKU's wordt beheerd, blijkt inefficiënt wegens de toenemende complexiteit van de sector. Het is echter mogelijk om de bevoorrading te plannen en te profiteren van de voordelen van deze methode met behulp van een WMS.
Easy WMS beschikt over geavanceerde functies voor geïntegreerd voorraadbeheer, en kan werken met verschillende bevoorradingsregels. Wilt u meer informatie over ons WMS, neem dan contact met ons op. Eén van onze experts zal u in detail uitleggen hoe deze software kan bijdragen tot een optimaal beheer van uw magazijn.