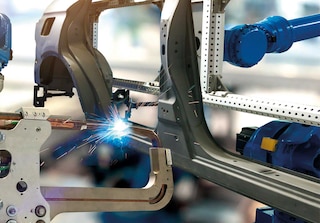
MRP: een belangrijke fase in het productieproces
De material requirements planning is een complexe logistieke uitdaging voor elke installatie. Hoeveel grondstoffen zijn er nodig, wanneer zijn ze nodig, of hoeveel eenheden moeten er geproduceerd worden, zijn enkele van de vragen die producenten al tientallen jaren beantwoorden met het MRP system (Material Requirements Planning).
In dit artikel wordt een analyse gemaakt van alles wat te maken heeft met de material requirements planning: de definitie ervan, hoe het werkt, de voordelen ervan en waarom het zo belangrijk was en nog steeds is, in het productieproces. Daarnaast wordt het verschil uitgelegd tussen een MRP system en een ERP.
Wat is een MRP?
De Material Requirements Planning is een systeem dat is ontworpen om de productieprocessen te beheren en de activiteiten van productie, inkoop en levering van het eindproduct van tevoren te coördineren.
Het MRP system werd in de jaren 1970 geïntroduceerd en heeft een snelle groei doorgemaakt. Het is ontleend aan het boek «Production Planning and Control: A Comprehensive Approach», geschreven door D.R. Kiran in 1975. Naar schatting maken reeds 700 ondernemingen gebruik van het MRP system om de productieprocessen te optimaliseren. Dit aantal steeg met 174% per jaar en bereikte in 1981, in slechts zes jaar, 8.000 ondernemingen.
Vandaag de dag wordt het MRP system beschouwd als zijnde de basis van de huidige computerprogramma's, die industriële processen optimaliseren: MRP II (Manufacturing Resource Planning), ERP (Enterprise Resource Planning), CRM (Customer Relationship Management), SRM (Supplier Relationship Management) ou MES (Manufacturing Execution System).
Material Requirements Planning MRP regelt de productieactiviteiten en optimaliseert het voorraadbeheer op basis van de bedrijfsbehoeften. Material Requirements Planning stelt elke producent in staat zijn hoofddoel te bereiken: te allen tijde over de juiste hoeveelheid middelen beschikken om de producten te produceren en deze binnen de kortst mogelijke tijd en tegen de laagst mogelijke kosten bij de klanten af te leveren.
Hoe werkt een MRP system?
Voor het MRP system is de invoer van gegevens van essentieel belang:
- Het hoofdproductieplan: bekend als het MPS (Master Production Schedule), geeft het aantal artikelen aan dat zal worden geproduceerd en binnen welke termijn.
- BOM: de Bill Of Materials geeft de hoeveelheden grondstoffen en de productieprocessen aan, die nodig zijn om één eenheid van het eindproduct te verkrijgen.
- De inventaris: bevat gedetailleerde informatie over de voorraad: zoals bijvoorbeeld de beschikbare voorraad, de bestelde voorraad, de geannuleerde bestellingen, en de doorlooptijd. Het doel is te weten welke grondstoffen beschikbaar zijn, zodat deze onmiddellijk kunnen worden gebruikt.
Met al deze gegevens voorhanden, biedt de ERP de volgende informatie:
- Het aanbevolen hoofdproductieplan: stelt een planning op met de begin- en einddatum van het productieproces, de benodigde hoeveelheden voor elke fase van het productieproces en de stuklijst oftewel de Bill Of Materials (BOM). Dit alles is bedoeld, om te voldoen aan de vraag die in het hoofdproductieplan is opgenomen.
- Het aanbevolen inkoopprogramma: het geeft de data aan waarop het ingekochte materiaal binnenkomt, en de data waarop de nieuwe bestellingen moeten worden klaargezet om samen te vallen met het hoofdproductieplan.
Het MRP system zorgt er derhalve voor dat het nodige materiaal wordt ontvangen om een minimale voorraad aan te houden ten behoeve van het productiecentrum, terwijl een efficiënte planning van productie, inkoop en levering van materialen gewaarborgd is.
Voorbeeld van material requirements planning
Na het opstellen van het hoofdproductieplan en de stuklijst, wordt bepaald dat voor de vervaardiging van een eindproduct (product X), 2 eenheden van materiaal A en 1 eenheid van materiaal B nodig zijn. Voor elke eenheid van A zijn 3 eenheden van materiaal C nodig, en voor elke eenheid van B zijn 2 eenheden van materiaal C en 4 eenheden van materiaal D nodig.
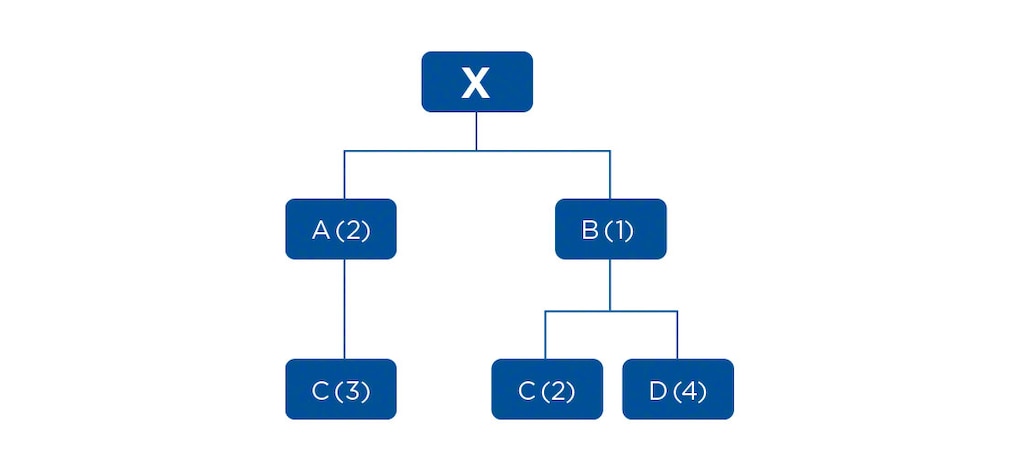
Hieronder volgt een gedetailleerde beschrijving van de inventarislijst IRF, (Inventory Record File), die de beschikbare voorraad en de doorlooptijd of lead time weergeeft voor de ontvangst van elk product:
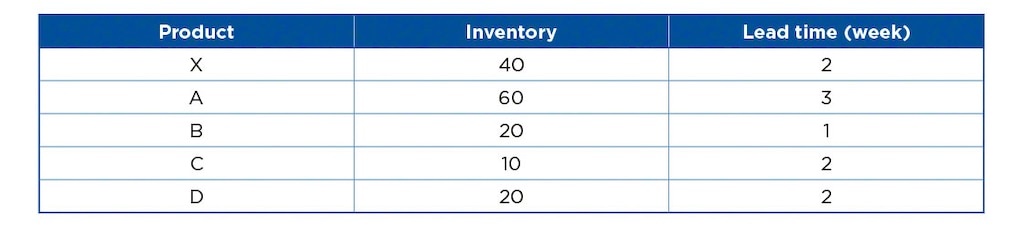
Hieronder volgt een samenvatting van een material requirements planning voor de vervaardiging van 100 stuks van product X in 10 weken:
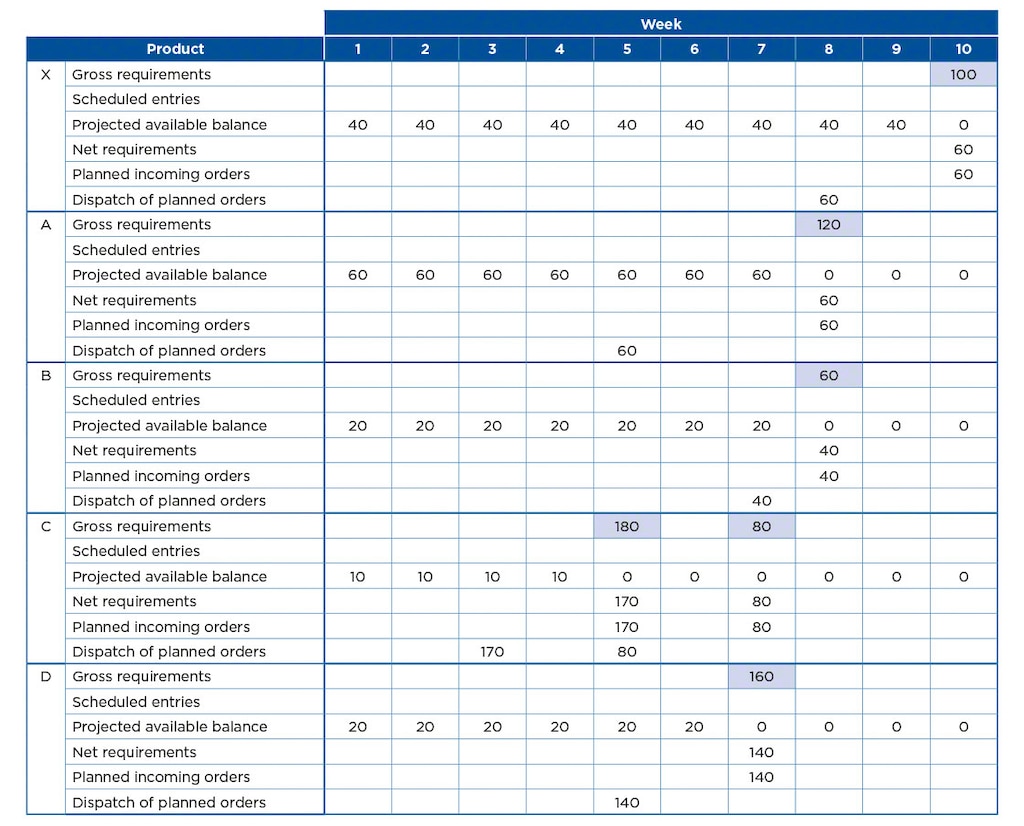
Hieruit blijkt dat om in week 10, over 100 stuks van product X te kunnen beschikken, 60 extra stuks nodig zijn, die moeten worden toegevoegd aan de 40 die reeds op voorraad zijn. Aangezien de doorlooptijd voor product X in de inventarislijst 2 weken bedraagt, moet de bestelling in week 8 geplaatst worden.
Als voor elke eenheid van product X 2 eenheden van A nodig zijn, dan zullen in week 8, 120 eenheden van A vereist zijn. Aangezien de voorraad reeds 60 eenheden telt, zal de nettobehoefte aan A ook 60 stuks bedragen. In verband met de doorlooptijd moeten de eenheden in kwestie drie weken van tevoren worden aangevraagd.
De nettobehoeften voor de producten B, C, D en F, worden volgens dezelfde procedure vastgesteld, evenals de week waarin deze moeten worden aangevraagd
De functies van een MRP en de voordelen van het gebruik ervan
Binnen een productieproces bestaat de functie van material requirements planning, uit het berekenen van de hoeveelheid benodigde grondstoffen, de benodigde componenten en de hoeveelheid eindproducten die gemaakt zullen worden.
Een MRP system biedt de volgende voordelen:
- Volledige beschikbaarheid van de grondstoffen voor de productie.
- Naleving van de leveringstermijnen.
- Het aanhouden van een minimale voorraad, zowel van grondstoffen als afgewerkte producten.
- Planning van de productieactiviteiten, de afleveringsbonnen en de inkooporders.
- Kostenbesparingen.
Een MRP system biedt een oplossing voor de dagelijkse problemen van producenten, met name op het gebied van de inkoop van grondstoffen. Een verkeerde of onvoldoende inkoop kan leiden tot langere leveringstijden en de aankoop van overtollig materiaal leidt tot extra opslagkosten.
Het verschil tussen MRP en MRP2
Begin jaren 80, heeft het MRP system (Material Requirements Planning) zich ontwikkeld tot MRP2 (Manufacturing Resource Planning), een geavanceerd planningssysteem met een breder toepassingsgebied. De belangrijkste verschillen tussen de beide systemen:
- Naast de material requirements planning integreert MRP2 andere activiteiten van de onderneming, zoals bijvoorbeeld de commerciële en financiële activiteiten.
- Terwijl MRP werkt volgens het hoofdproductieplan, is MRP2 gebaseerd op de vraag en marktonderzoek.
- MRP2 analyseert het functioneren van de onderneming met het oog op een efficiënte planning, terwijl MRP dit doet aan de hand van de praktijk en eerdere bedrijfservaringen.
- De Material Requirements Planning (MRP) is een open systeem, dit in tegenstelling tot MRP2, dat gesloten is. Dit betekent dat MRP2 rekening kan houden met de rapporten die het opstelt, en dus een nieuwe planning kan uitvoeren die meer in overeenstemming is met de realiteit.
MRP2 is de moderne versie van MRP. Het geeft niet alleen antwoord op de vraag hoeveel er moet worden geproduceerd en wanneer, maar bepaalt ook de benodigde middelen en tijd die daartoe aangewend moeten worden.
Verschillen tussen MRP en ERP
De Enterprise Resource Planning werd voor het eerst gebruikt in de jaren negentig en is uitgebreider en veelzijdiger dan zijn voorgangers. Het feit dat het alle taken van de onderneming in één enkel systeem kan onderbrengen, is het kenmerkende element ervan waardoor het zich onderscheidt van MRP.
Met andere woorden, MRP is een op zichzelf staande software, terwijl ERP de computersystemen die door elke afdeling worden gebruikt, integreert en combineert tot een gecentraliseerde database. Hierdoor kan elke afdeling in het bedrijf in real-time toegang krijgen tot de beschikbare informatie, workflows controleren, vergissingen tot een minimum beperken en gegevens uitwisselen met andere afdelingen.
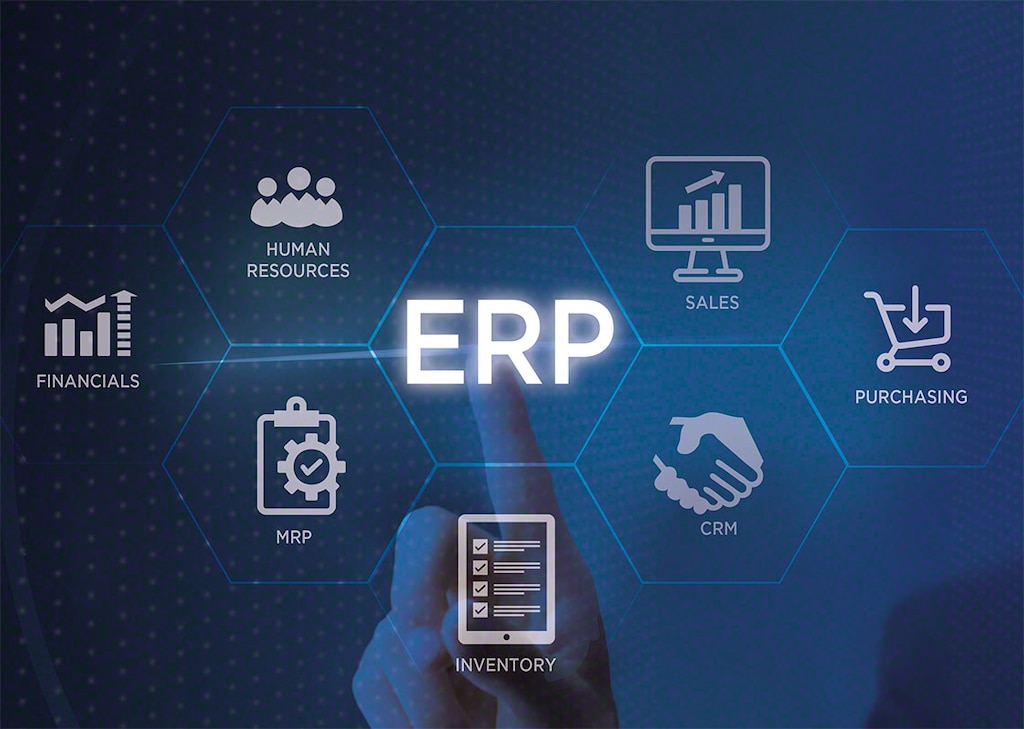
Het MRP system: in het voetspoor van de technologische vooruitgang
Na vijftig jaar kan met recht worden geconcludeerd dat de material requirements planning een keerpunt in het productieproces heeft ingeluid. Om de rentabiliteit van de bevoorradingsketen te verbeteren, is de planning van de behoeften aangepast aan de nieuwe technologieën.
Bij Mecalux wordt voortdurend gewerkt aan de meest geavanceerde technologische oplossingen op de markt, zowel voor wat betreft de opslag als het logistiek beheer, zoals het geval is bij Easy WMS. Dit systeem kan worden geïntegreerd met willekeurig welke ERP, waardoor de twee systemen gegevens en informatie kunnen uitwisselen om een grotere productiviteit in het magazijn te bereiken.
Neem contact met ons op, onze experts geven u graag advies en helpen u het beste uit uw toeleveringsketen of Supply Chain te halen.